Home / Tech Resource Articles / Product Resources /
PennMet 2000
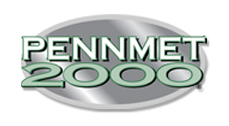
Penn Stainless Products offers a unique product for the machining industry – in stainless steel Round, Square and Hex bars. Our proprietary grades of stainless steel machining bars in 304/L and 316/L are melted to a uniquely controlled chemistry to produce optimal machining characteristics: faster cutting speeds, reduced tool wear, and lower cost parts.

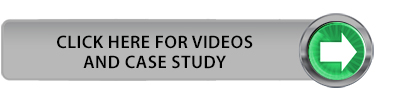
PennMet 2000 – Superior Stainless
- Improved Machinability
- Consistent Performance from Lot to Lot
- Improved Surface Finish
- Increased Feeds and Speeds
- Superior Chip Control
- Longer Tool Life
Machining Operations
Turning | Milling | Drilling | Threading |
Forming – HSS and carbide | Sawing | Parting Off |
Improved Machinability:
PennMet 2000 – A SPECIAL PROCESS FOR A SPECIAL STEEL QUALITY
- Process applied austenitic stainless steel bar resulting in optimal machinability.
- Meets all standard specifications requirements of ASTM & ASME for applicable grades.
- Ladle metallurgy to control composition, amount, size, shape and distribution of nonmetallic inclusions.
- Can machine at higher speeds and feeds – increase size of machining window.
V1000 – Machining test showing cutting speed that gives a tool lifetime of 1000mm drilled length.
PennMet Treatment
- Deoxidation during standard stainless steel melting results in comparatively large Al2O3 inclusions.
- Typically more than 1,000,000 inclusions/lb.
- These inclusions are very hard. For reference carbide tools are coated with Al2O3 for wear resistance.
- PennMet treatment improves the composition, size, shape and distribution of these inclusions.
Benefit of PennMet at Higher Speeds
Results of PennMet 304 vs Standard 304
PennMet works for drilling
0.030% Sulfur content helps but…Pre-treatment is more important
Problem – Higher tool wear and long production time
Solution – PM 2000 enabled the machines to increase feeds and speeds by 70% to 80% and reduce part wear. The customer saved $1.68 to $14.50 per component and increased overall productivity by 30% to 54%.
Sample Test A Report: Adapter, Rough OD Common 316/316L vs PennMet 316/316L
PENN STAINLESS TEST REPORT – DATE: 7/17/2014 | |||
---|---|---|---|
Turning | Rough Outside Diameter | Issued by: DNL | |
Machine: Mazak Dual Turn 20 | Machine #: 12 | Test #: 1 | |
Component: Housing | Material: PennMet 316/316L | Material: Common 316/316L | |
Operation: Rough Turn OD | Hardness, hB: 180 – 240 | Hardness, hB: 180 – 240 | % of increase |
Cutting Speed | 600 | 500 | 83% |
RPM | 1150 | 950 | 83% |
Feed/rev. | 0.013 | 0.01 | 77% |
Depth of Cut | 0.007 | 0.035 | 50% |
Length of Cut | 7 | 14 | 200% |
Criterion tool change | Flank | Flank | |
Machine Cost/Hour | $100.00 | $100.00 | |
Cutting time/component (mins) | 0.47 | 1.47 | 315% |
Non cutting time/component (mins) | 2 | 2 | |
No. of components/set of edges | 25 | 12 | |
Tool changing time (mins) | 2 | 2 | |
Total time/component (mins) | 2.55 | 3.64 | 30% |
Machine cost/component | $4.11 | $5.79 | 29% |
Total machining cost/component | $4.11 | $5.79 | 29% |
Productivity increase % | 30% | ||
Savings/component | $1.68 |
Sample Test B Report: Housing, Rough Turn OD Common 316/316L vs PennMet 316/316L
Penn Stainless Test Report – Date: 7/18/2014 | |||
---|---|---|---|
Turning | Outside Diameter | Issued by: DNL | |
Machine: Okuma LB 25 | Machine #2 | Test #1 | |
Component: Housing | Material: PennMet 316/316L | Material: Common 316/316L | |
Operation: Rough Turn OD | Hardness, hB: 180 – 240 | Hardness, hB: 180 – 240 | % of increase |
Cutting Speed | 450 | 300 | 67% |
RPM | 215 | 145 | 67% |
Feed/rev. | 0.011 | 0.008 | 73% |
Depth of Cut | 0.15 | 0.1 | 67% |
Length of Cut | 10 | 15 | 150% |
Criterion tool change | Flank | Flank | |
Machine Cost/Hour | $100.00 | $100.00 | |
Cutting time/component (mins) | 4.23 | 12.93 | 306% |
Non cutting time/component (mins) | 3 | 3 | |
No. of components/set of edges | 4 | 2 | |
Tool changing time (mins) | 2 | 2 | |
Total time/component (mins) | 7.73 | 16.93 | 54% |
Machine cost/component | $12.05 | $26.55 | 55% |
Productivity increase % | 54% | ||
Savings/component | $14.50 |